Lecture 3D Geometry Processing
Scanning and Fabrication
Prof. Dr. David Bommes
Computer Graphics Group
3D Content Creation Pipeline
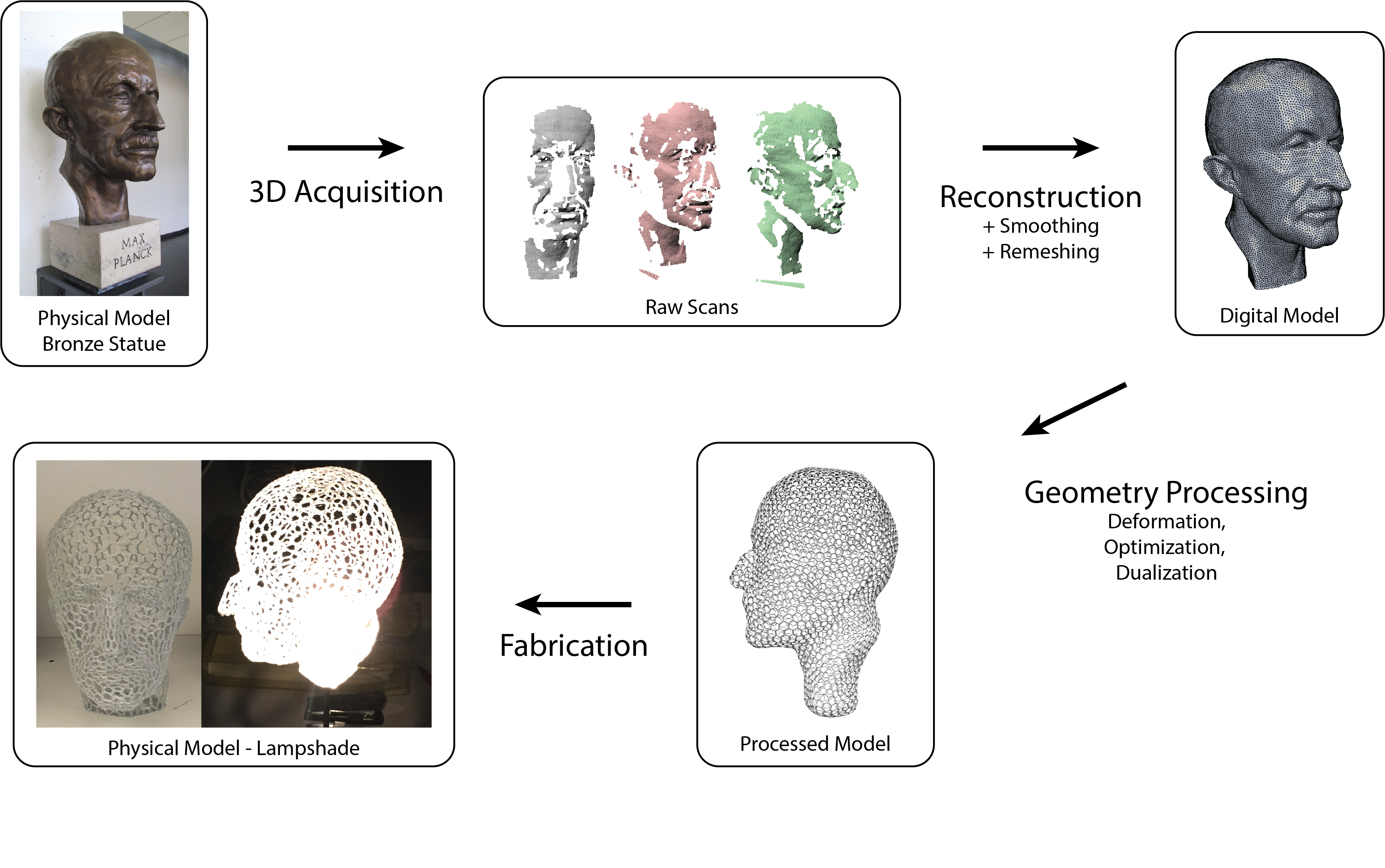
3D Content Creation Pipeline
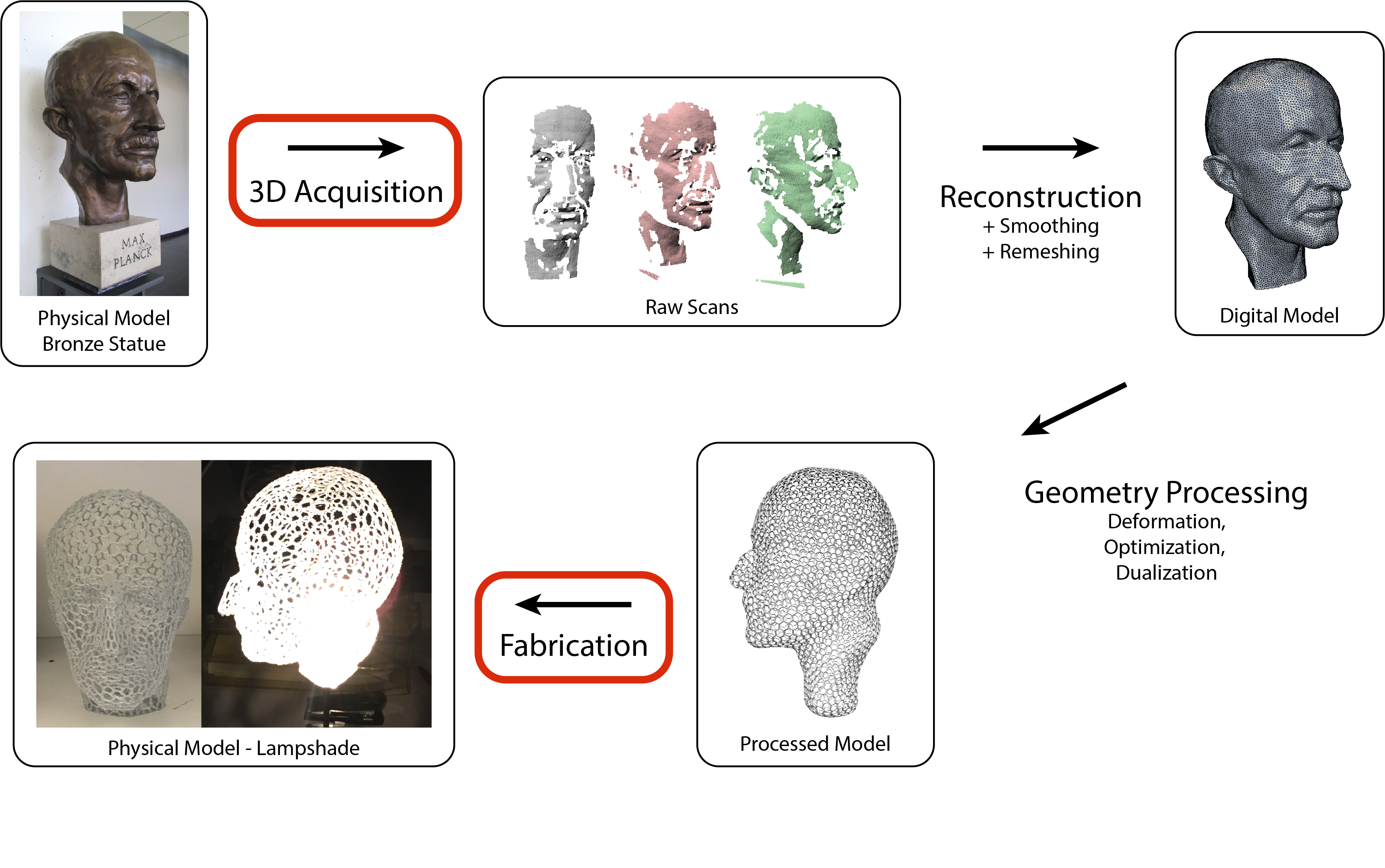
3D Content Creation Pipeline
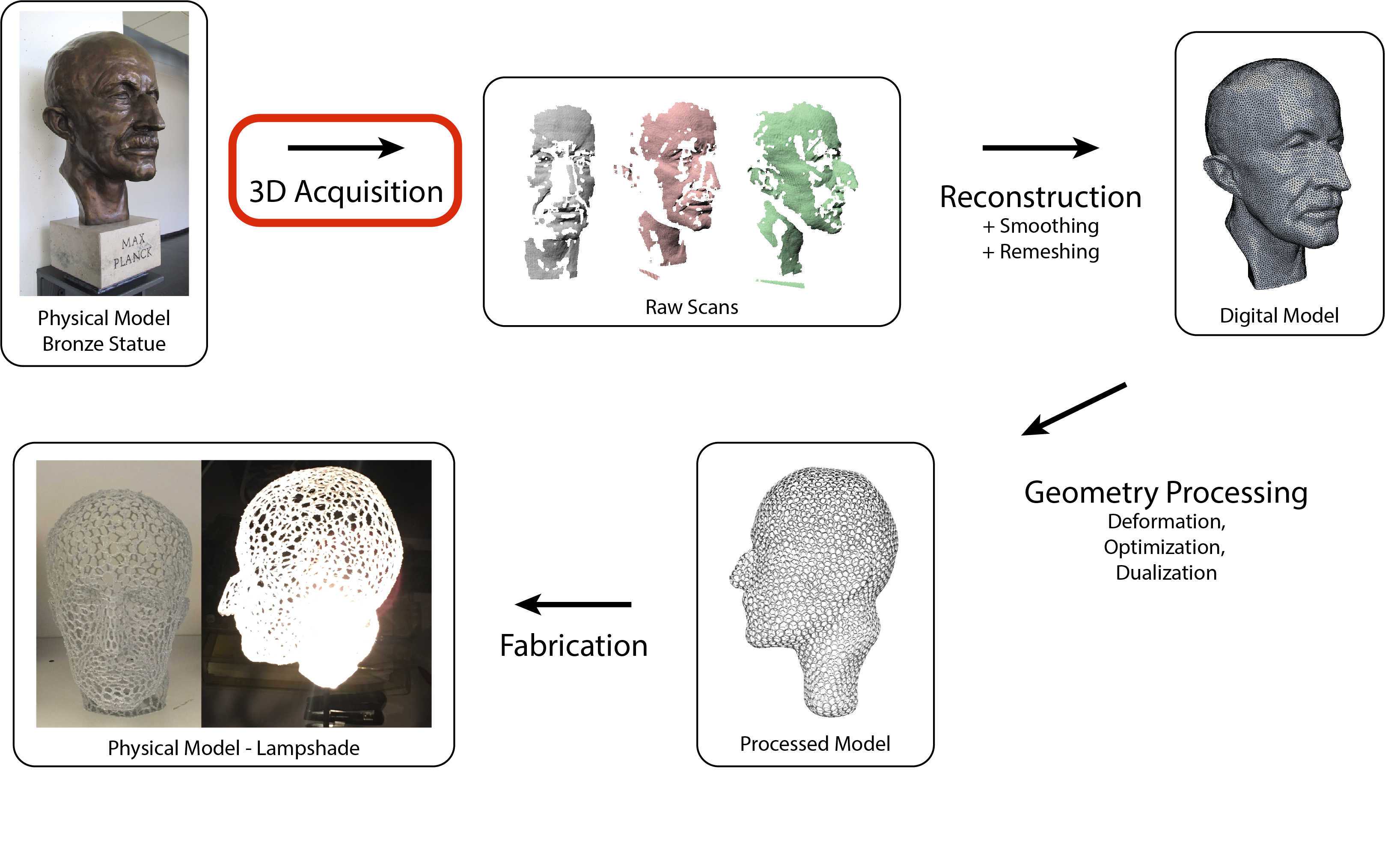
Digital Michelangelo Project
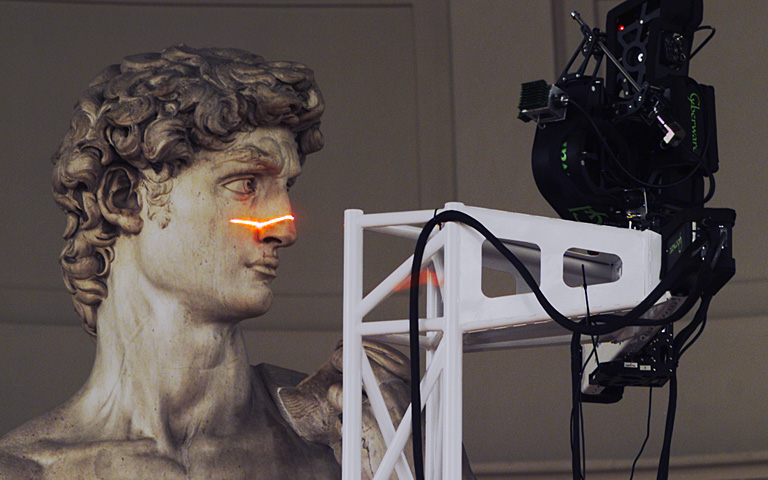
- Scan large statues (~5m) at high resolution (1/4 mm)
- Capture chisel marks
- Record color/reflectance for re-lighting
Digital Michelangelo Project
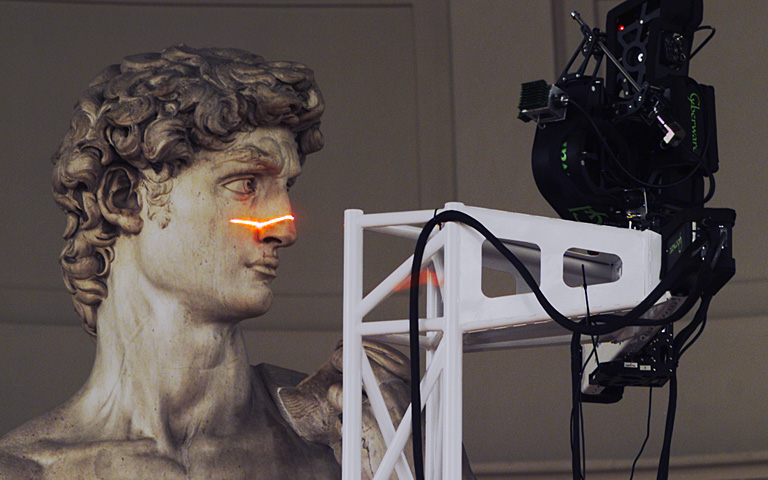
- Several challenges
- Fragile, precious sculptures
- Bulky equipment
- Visibility
Digital Michelangelo Project
1G sample points
8M triangles
4G sample points
8M triangles
- Another major challenge: huge data sets!
Aachen Dome
3D Scanning Techniques

3D Scanning Techniques

Time-of-Flight Scanners
- Probe object by laser or infrared light
- Emit pulse of light and measure the time until the reflection from the surface is “seen” by a detector
- Speed of light & measured round-trip time ==> distance to surface
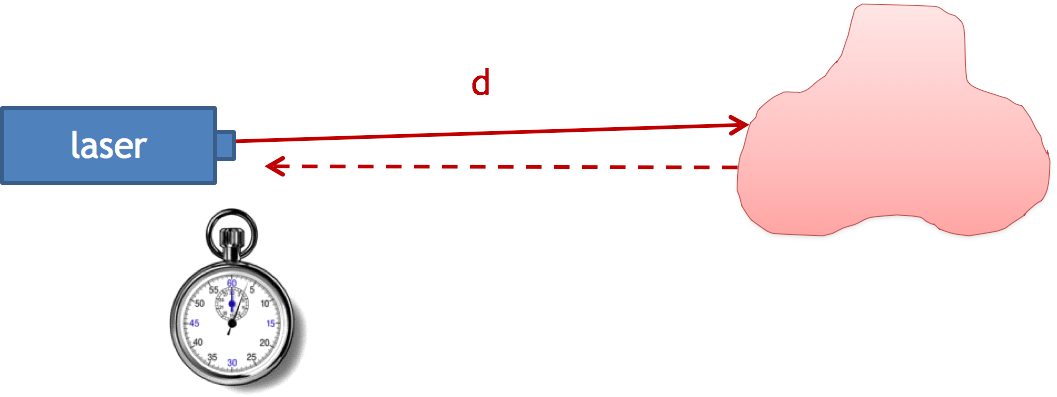
Time-of-Flight Scanners
- Capturing a full surface
- Sweep beam over the surface, or
- Use time-of-flight camera
- High speed of light makes accurate measurement difficult
SwissRanger by Mesa
Kinect One
Time-of-Flight Scanners
- Laser LIDAR
- Light Detection and Ranging
- Good for long distance scans
- 6mm accuracy at 50m distance
Forecast 3D Laser System
3D Scanning Techniques

Triangulation Principle
- Two “cameras” identify the same 3D point
- Compute depth from angles and baseline
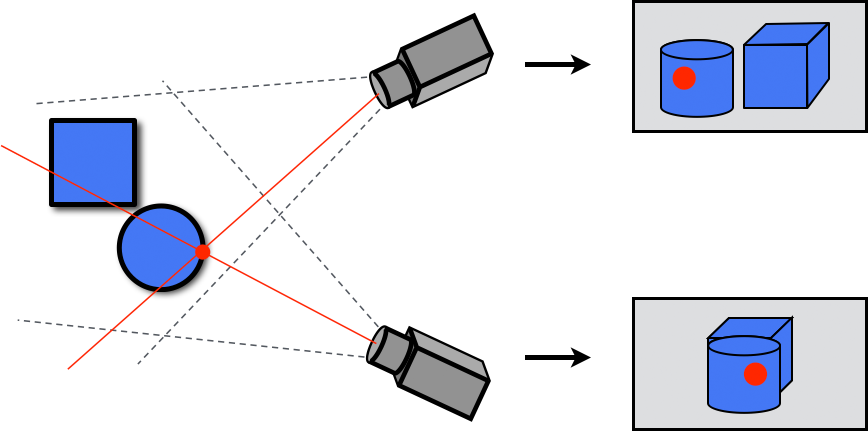
Triangulation Principle
- Two “cameras” identify the same 3D point
- Compute depth from angles and baseline
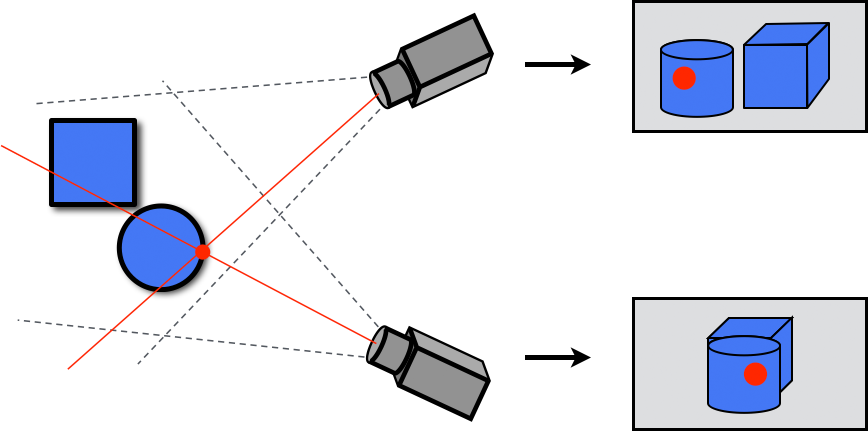
- Passive Stereo Matching
- Find and match features in both images
Passive Stereo Matching
- With high resolution cameras, skin has a lot of details!
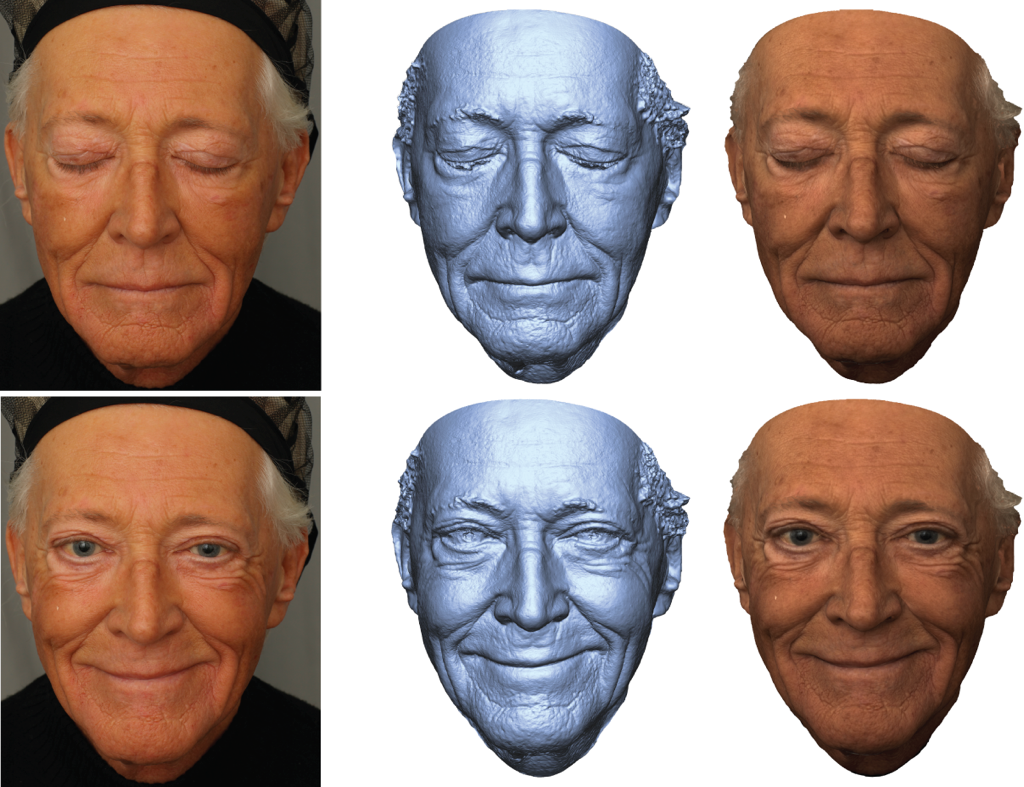
Passive Stereo Matching
- Passive stereo capturing is fast (just one shot)
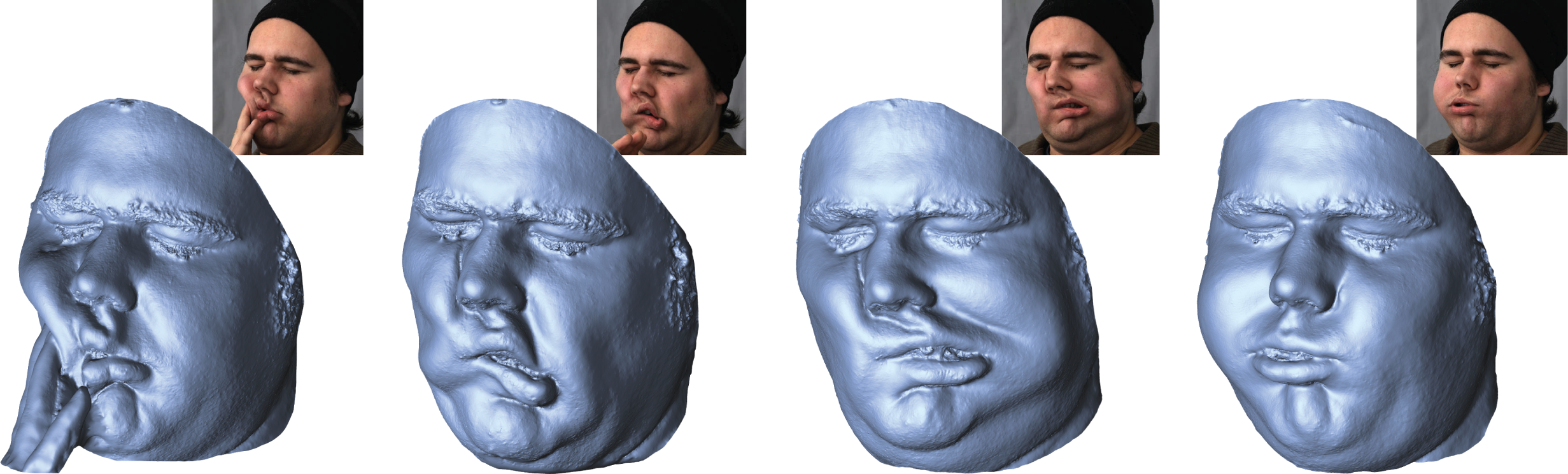
Ten24 Face Scanning
Ten24 Face Scanning
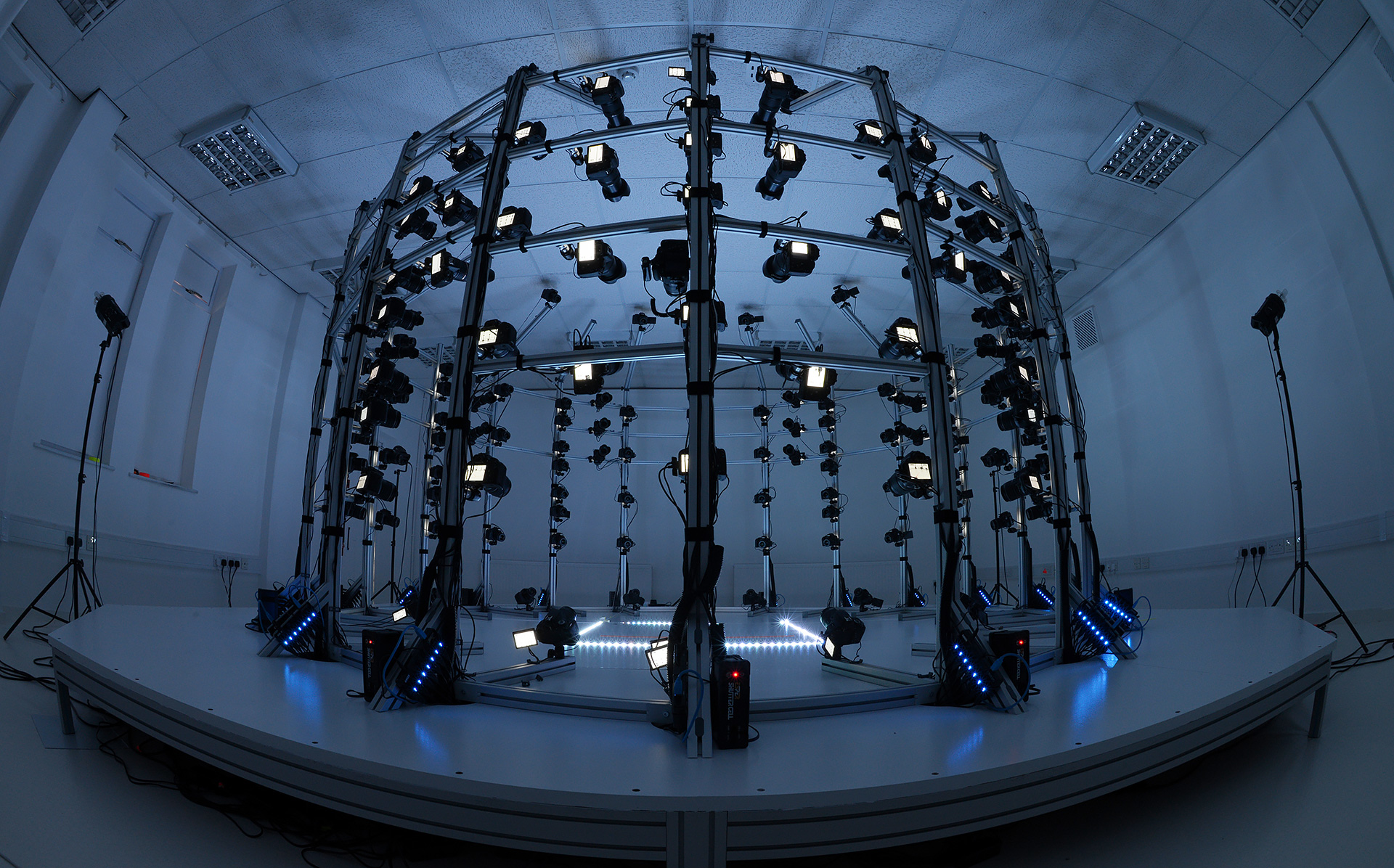
- More than two cameras!
- Same triangulation principle: one camera pair at a time.
Multi-view Stereo
3D Scanning Techniques

Structured Light Scanner
- 1 camera and 1 projector
- Project special patterns to identify pixels
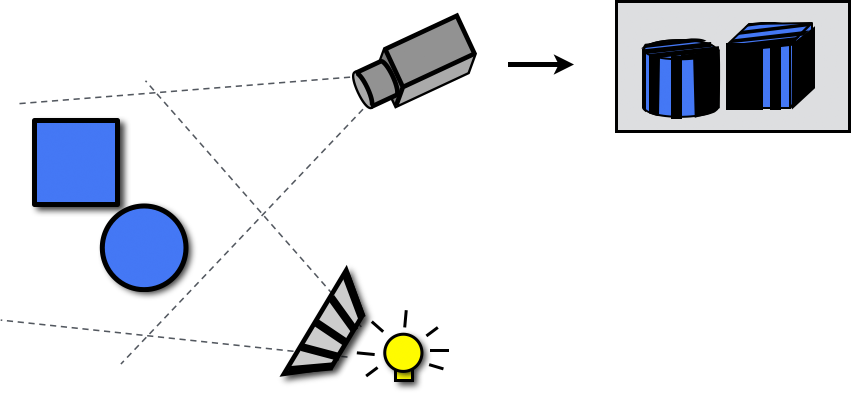
Structured Light Scanner
- 1 camera and 1 projector
- Project special patterns to identify pixels
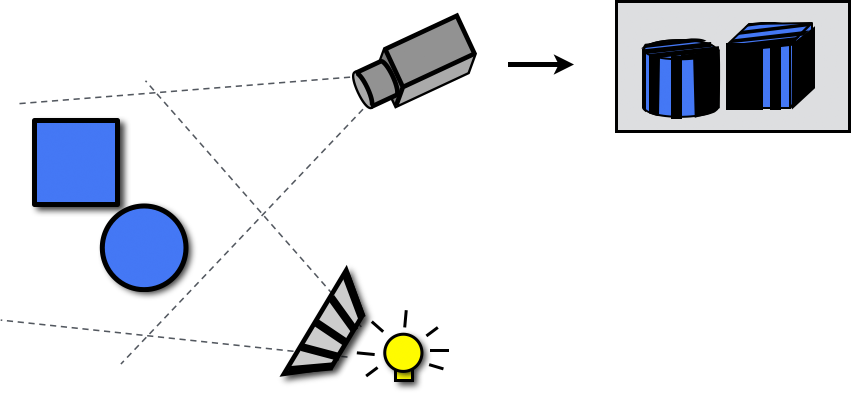
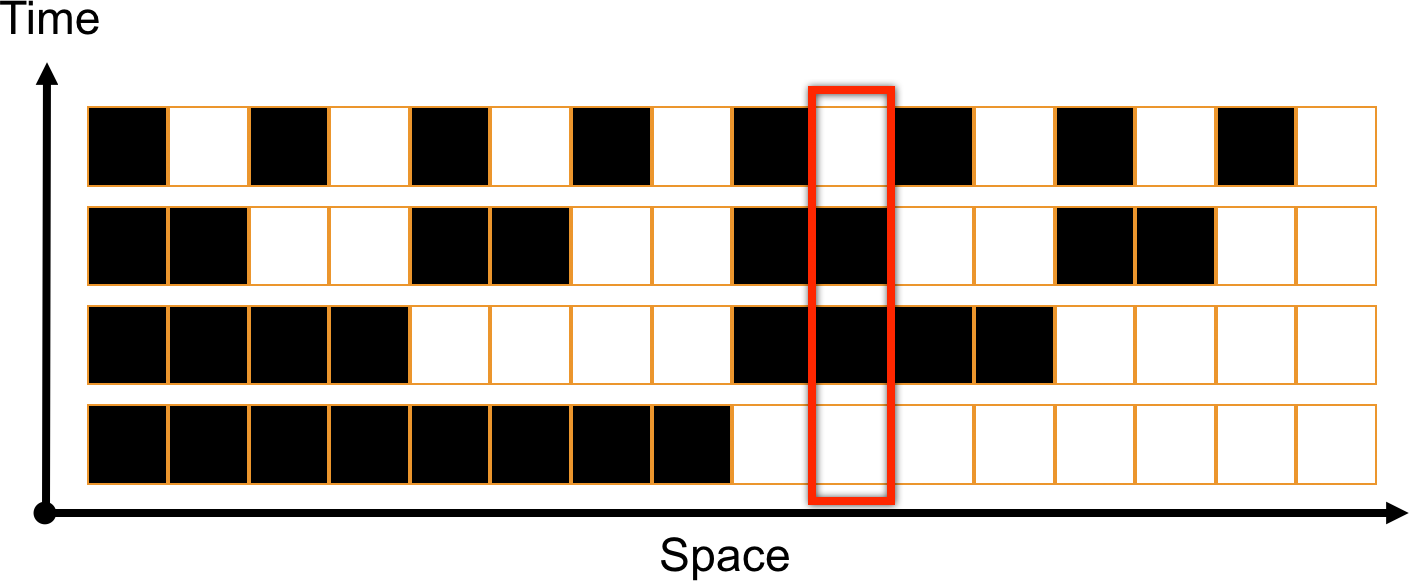
Structured Light Scanner
- Consumer-level scanner: e.g. Microsoft Kinect
- Project infrared pattern, but just one frame
- Fast (30fps), but noisy data
infrared pattern
[Denis John]
Structured Light Scanner
- Comparison to custom-built scanner (>$10k)
LGG Lab Scanner (2009) 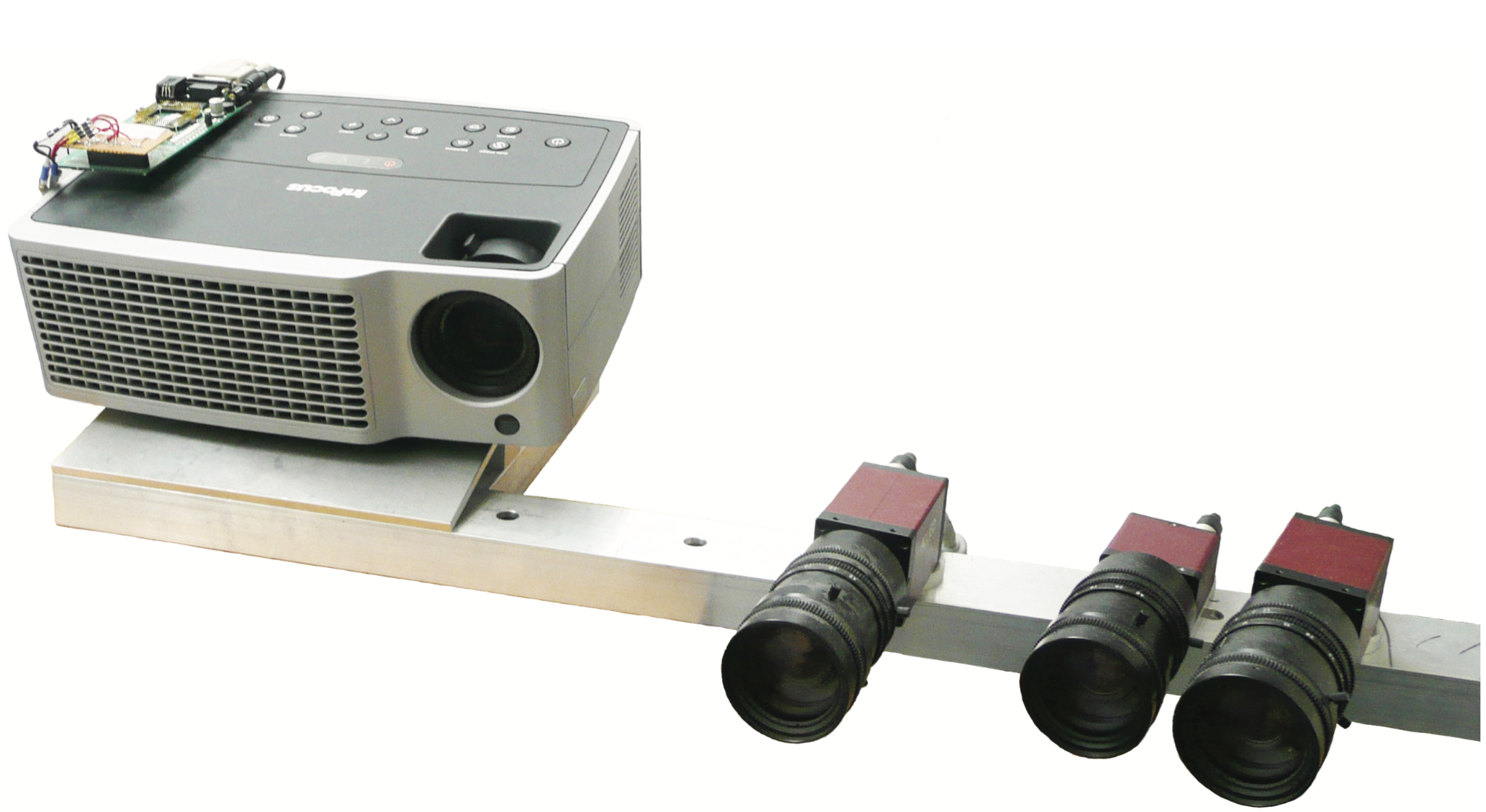
Kinect (2011) 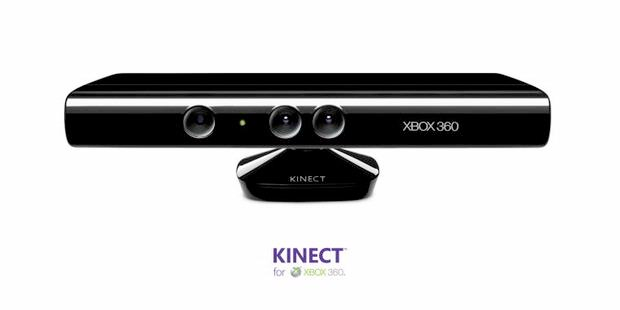
Aside: Face Tracking
LGG Research Prototype 2013
Aside: Face Tracking
LGG Spin-Off Company: Faceshift 2015
Aside: Face Tracking
Apple’s Animojis
FaceID
Apple’s FaceID
3D Scanning Techniques

Laser Scanning
- 1 camera and 1 laser beam
- Sweep laser, identify laser in camera image
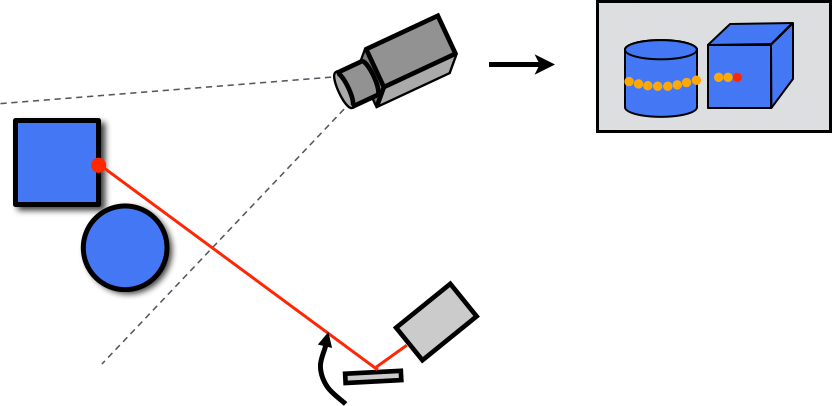
Digital Michelangelo Project
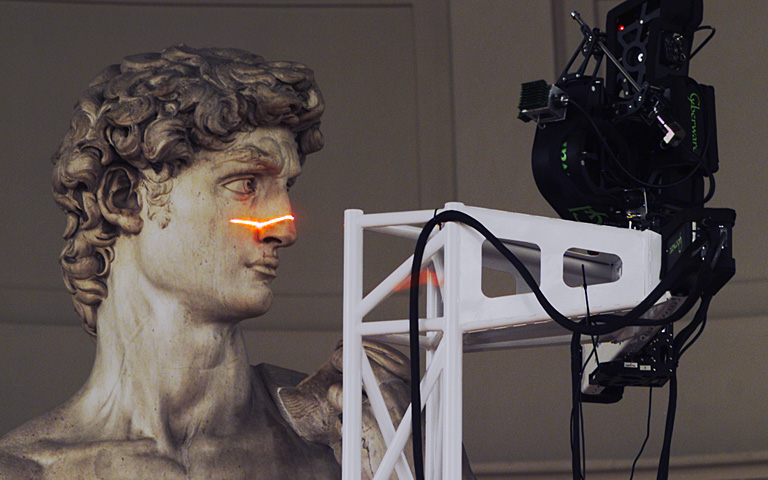
3D Scanning Techniques

3D Scanner Data
- Common issues with scanned data:
- Noise (especially bad with structured light scanning) Kinect (2011)
3D Scanner Data
- Common issues with scanned data:
- Noise (especially bad with structured light scanning)
- Holes
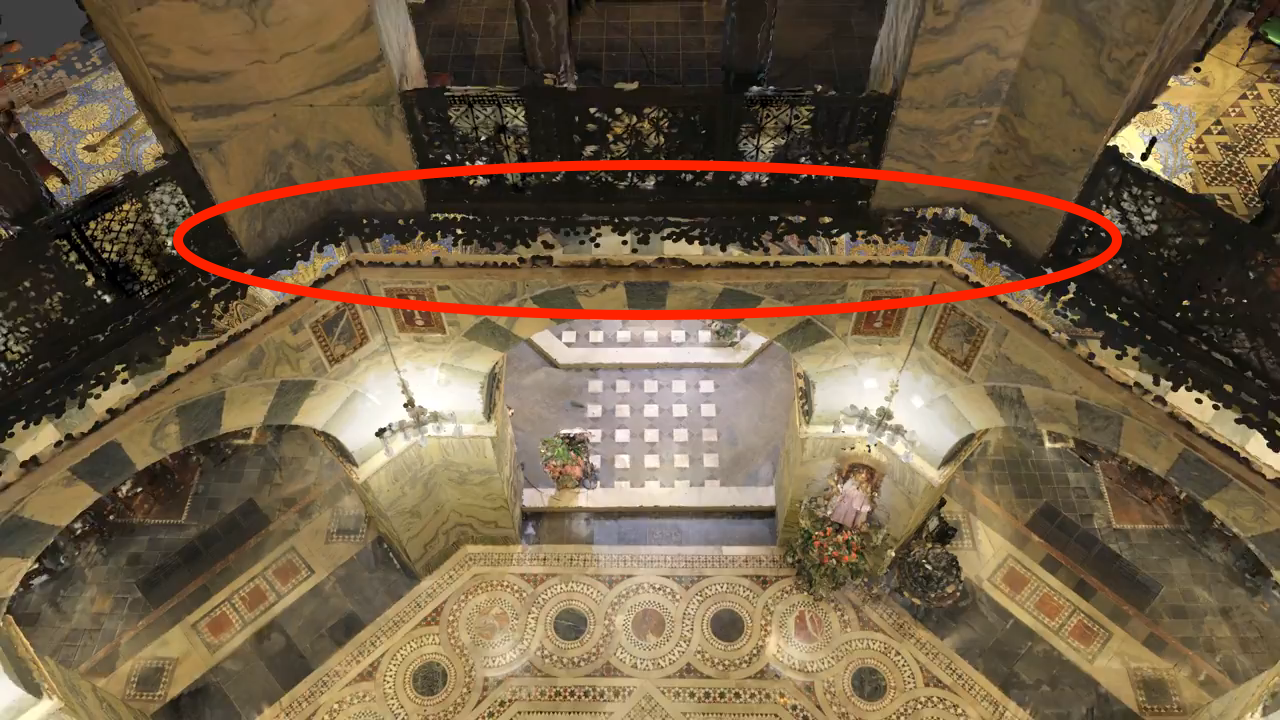
3D Scanner Data
- Common issues with scanned data:
- Noise (especially bad with structured light scanning)
- Holes
- Insufficient resolution

3D Content Creation Pipeline
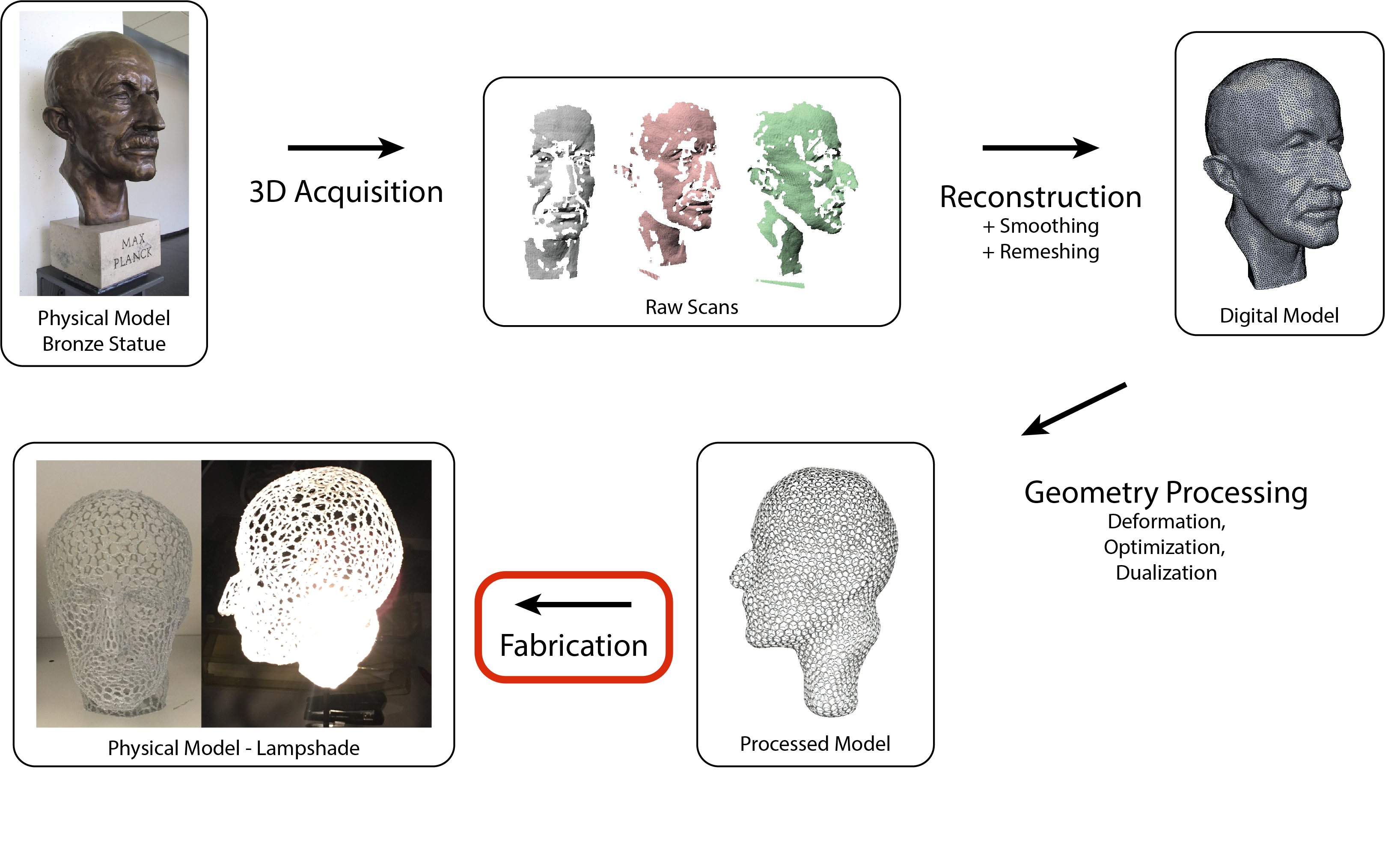
Digital fabrication: bringing digital geometry to the physical world
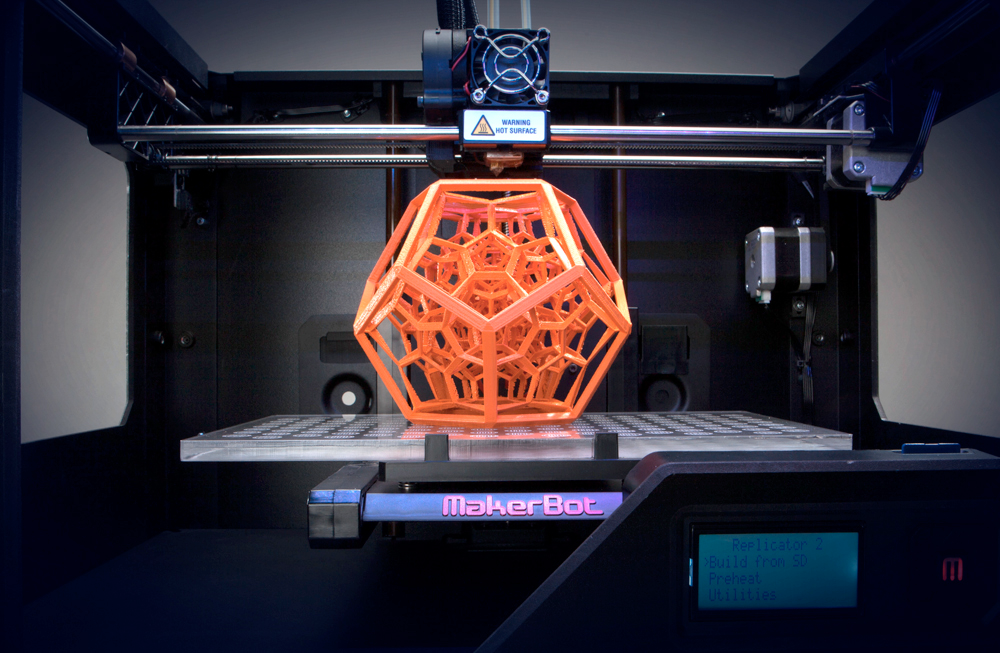
- Fabrication technologies
- Subtractive
- Laser cutting
- CNC (computer numerical control) turning/milling
- Additive
- Designing parts for 3d printing
Laser cutting
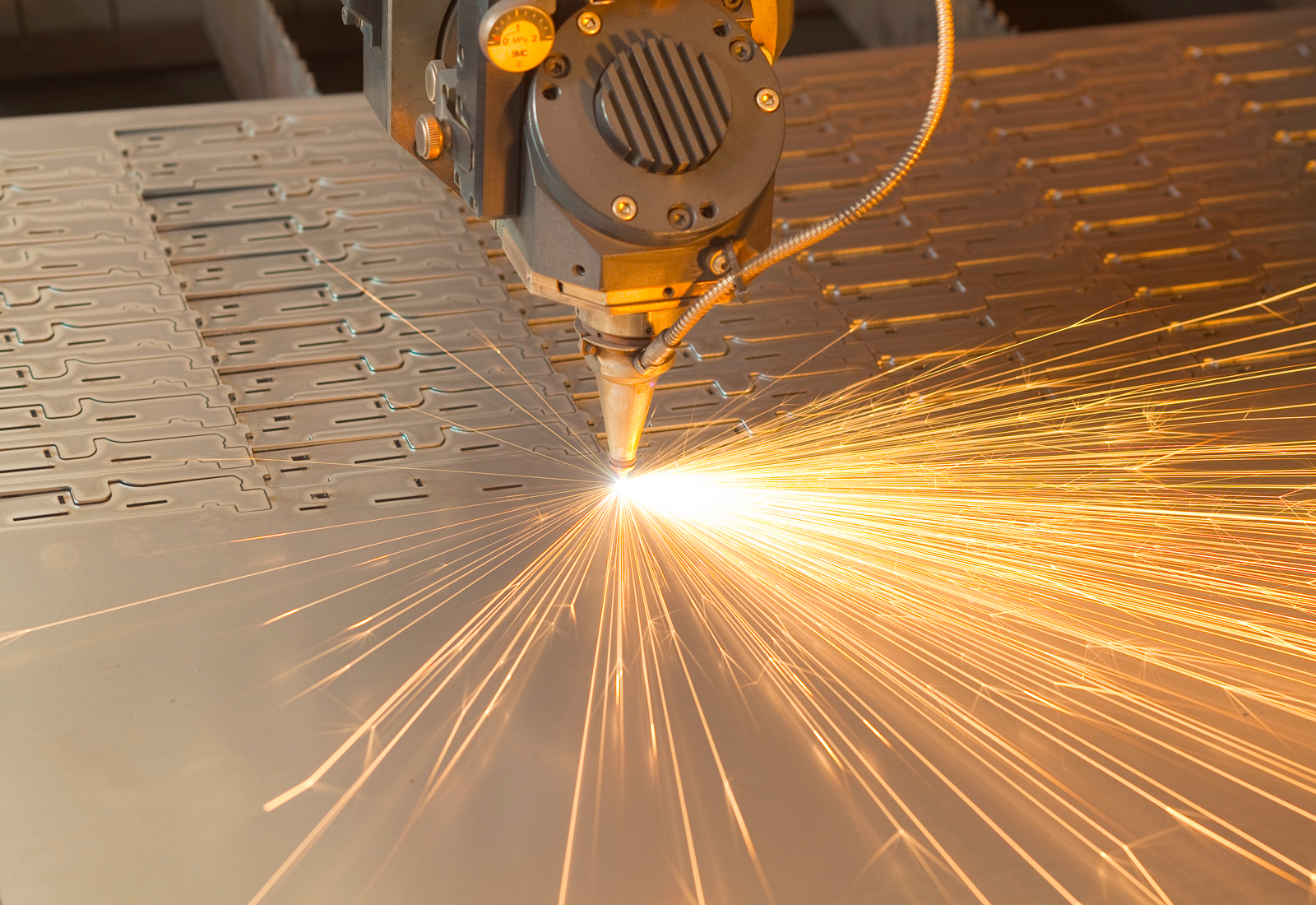
- Cut/engrave flat sheets with a laser
- Supports many materials (wood, metal, paper, acrylic, …)
Laser cutting
Laser cutting: how it works
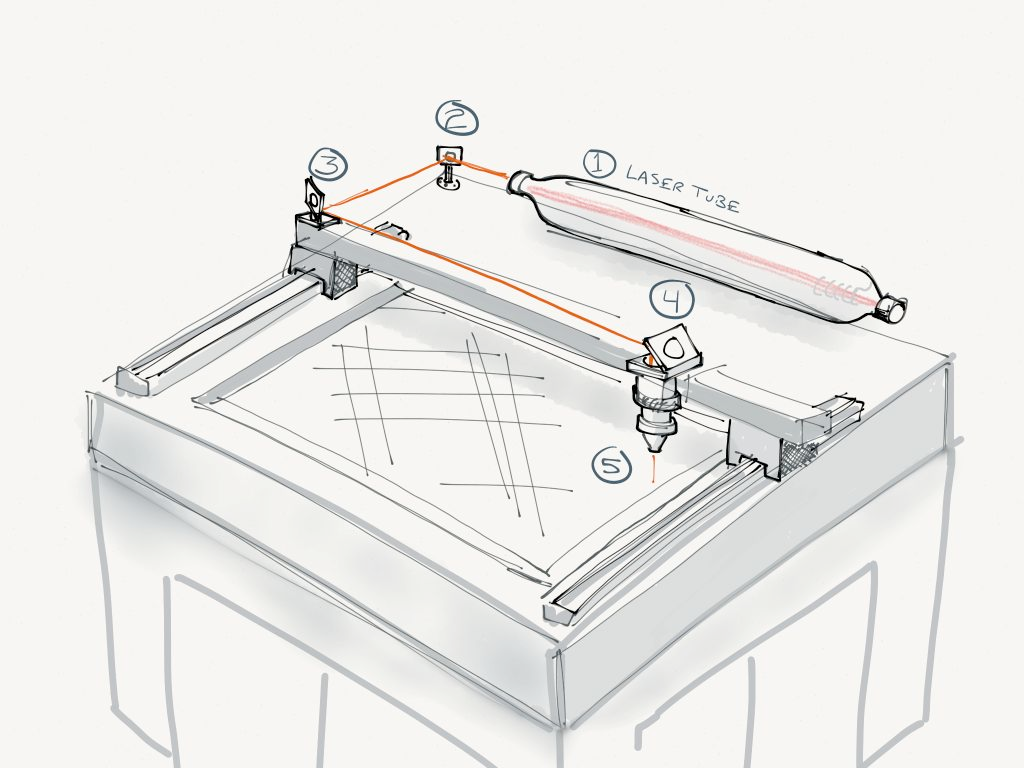
- Mirrors direct laser beam to precise (x, y) location
- Laser intensity/exposure time tuned for the material and desired effect (cutting vs engraving)
Laser cutting
Laser cutting: from file to object
- Design is just an image; mode chosen by color:
vector cutting, vector engraving, raster engraving
Laser cutting
- Great for fabricating 2D or 2.5D designs
- Can also produce 3D shapes:
Laser cutting: designing sliced parts
Rhino/Grasshopper
Laser cutting: 3D shapes by folding
Pepakura Designer
Laser cutting: curved surfaces
- Sheet metal/paper only bend into developable surfaces
(Gaussian curvature K = 0)
- Inserting cuts enables stretching, permitting nonzero K
Beyond Developable: Konakovic et al. 2016
CNC turning (lathes)
- Rapidly spin material, insert cutting tool
- Great for surfaces of revolution, screw threads, etc.
Glacern Machine Tools - YouTube
CNC milling
- Rotating cutter, complex insertion paths (5-axis)
- Produce much more general 3D shapes
CNC milling: advantages
- Great accuracy
- Large parts
- Great mechanical properties:
part is solid material, not built from slices
CNC milling: limitations
Wasteful: material milled away is lost
Geometry limitations:
cutting tool must reach all surfaces
Planning tool paths/selecting cutting tools can be challenging
- Higher fixed-costs
- Slower turnaround time
Usually large, expensive and dangerous
Infill Optimization: Wu et al. 2017
Desktop CNC milling
Pocket NC Version 2 - YouTube
3D printing
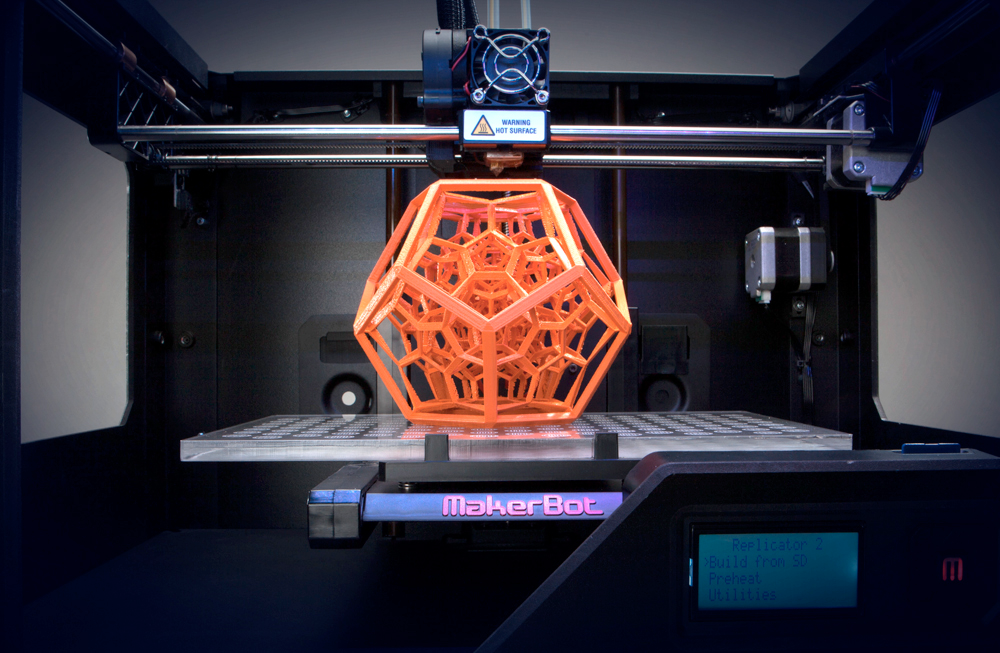
- Slice 3D object into many layers
- Fabricate layers one at a time, from bottom to top
3D printing: advantages
- Pay only for the material you use
- Material isn’t wasted like in CNC milling
- Cost and fabrication time independent of complexity
- Objects with highly complex topology can be fabricated
- “Just click print”
- Less complicated planning process than CNC
- Shorter turn-around time
Infill Optimization: Wu et al. 2017
Applications: industrial design
Rensselaer Polytechnic Institute
Applications: customized products
Makerbot
Makerbot
Applications: aerospace
Boeing 787 - Wikipedia
Titanium Part for 787 - Norsk Titanium
Boeing is saving $3 million on each 787 jet using 3D printing
(by avoiding material waste).
Applications: medical/dental
Robohand
Amos Dudley
Applications: new materials
James Zhou
Create new materials by printing microstructure
Applications: shoes
Adidas and Carbon3D
Spatially varying properties for optimal sports performance
Applications: mechanical clock!
Christoph Laimer - YouTube
3D printing: technologies
- Fused Deposition Modeling (FDM)
- Stereolithography (SLA)
- Selective Laser Sintering/Melting (SLS/SLM)
- Material Jetting (MJP)
- …
FDM technology
3D Hubs
Extrude melted plastic through a nozzle to form each layer
FDM limitations
- Lower resolution; limited by
- nozzle diameter
- spatial precision of extruder head
- flow of melted plastic
- Poor bonding between layers (anisotropic properties)
3D Hubs
SLA Technology
3D Hubs
Cure liquid resin into a solid by shining UV light
3D printing: DLP SLA (B9 Creator)
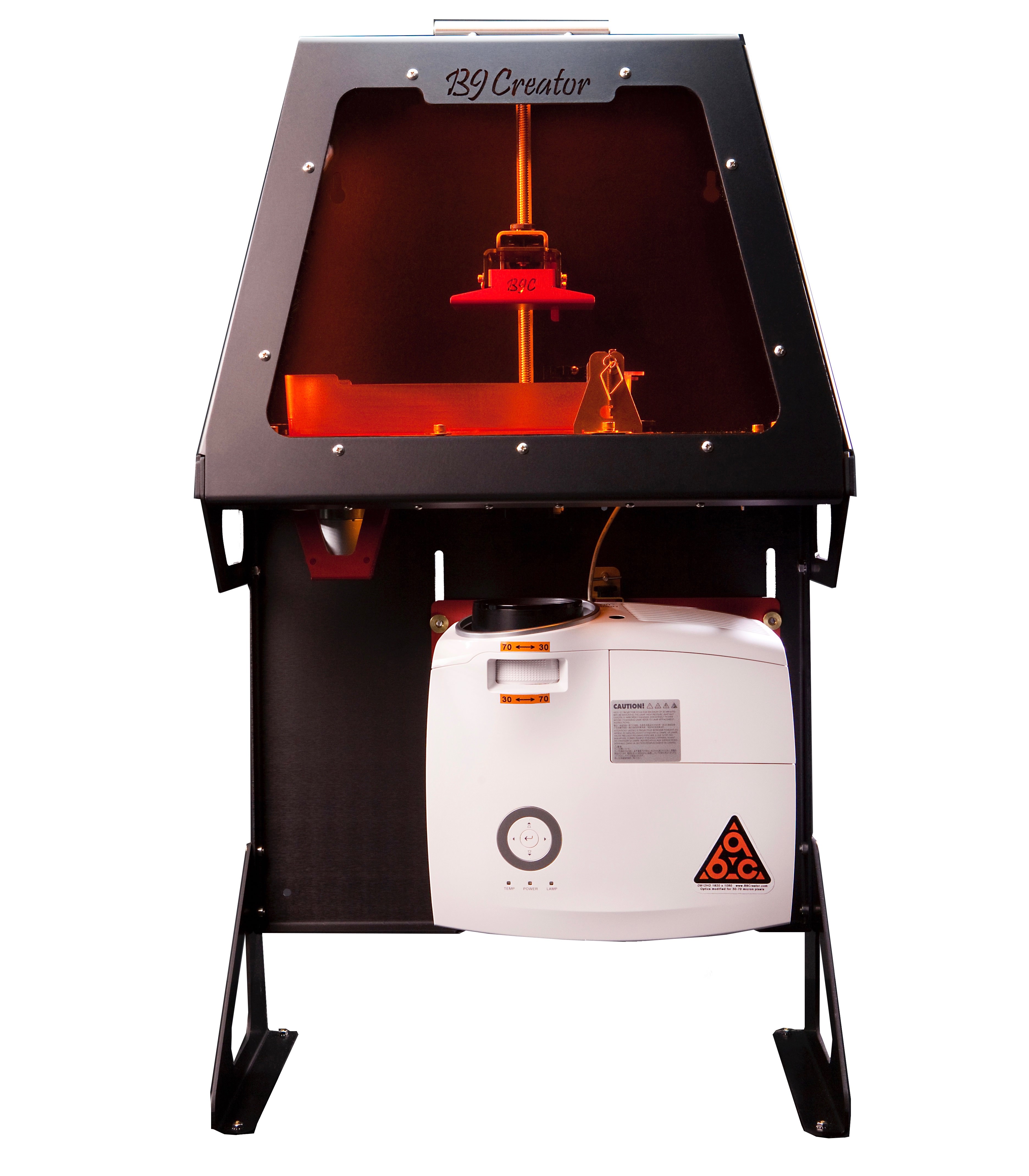
Project and cure entire layer geometry simultaneously
SLA pros and cons
- Advantages
- Excellent resolution (25um layer height)
- Layers almost perfectly bind; isotropic properties
- Wide range of resins to choose from
- Disadvantages
- Requires cleaning and curing postprocess (place in UV oven)
- Color and mechanical properties shift over time as curing continues
- Only one material at a time
SLS/SLM Technology
3D Hubs
Laser shines on a bed of plastic or metal powder, fusing or melting the particles into a solid part.
Material Jetting Technology
3D Hubs
3D printing: what can go wrong?
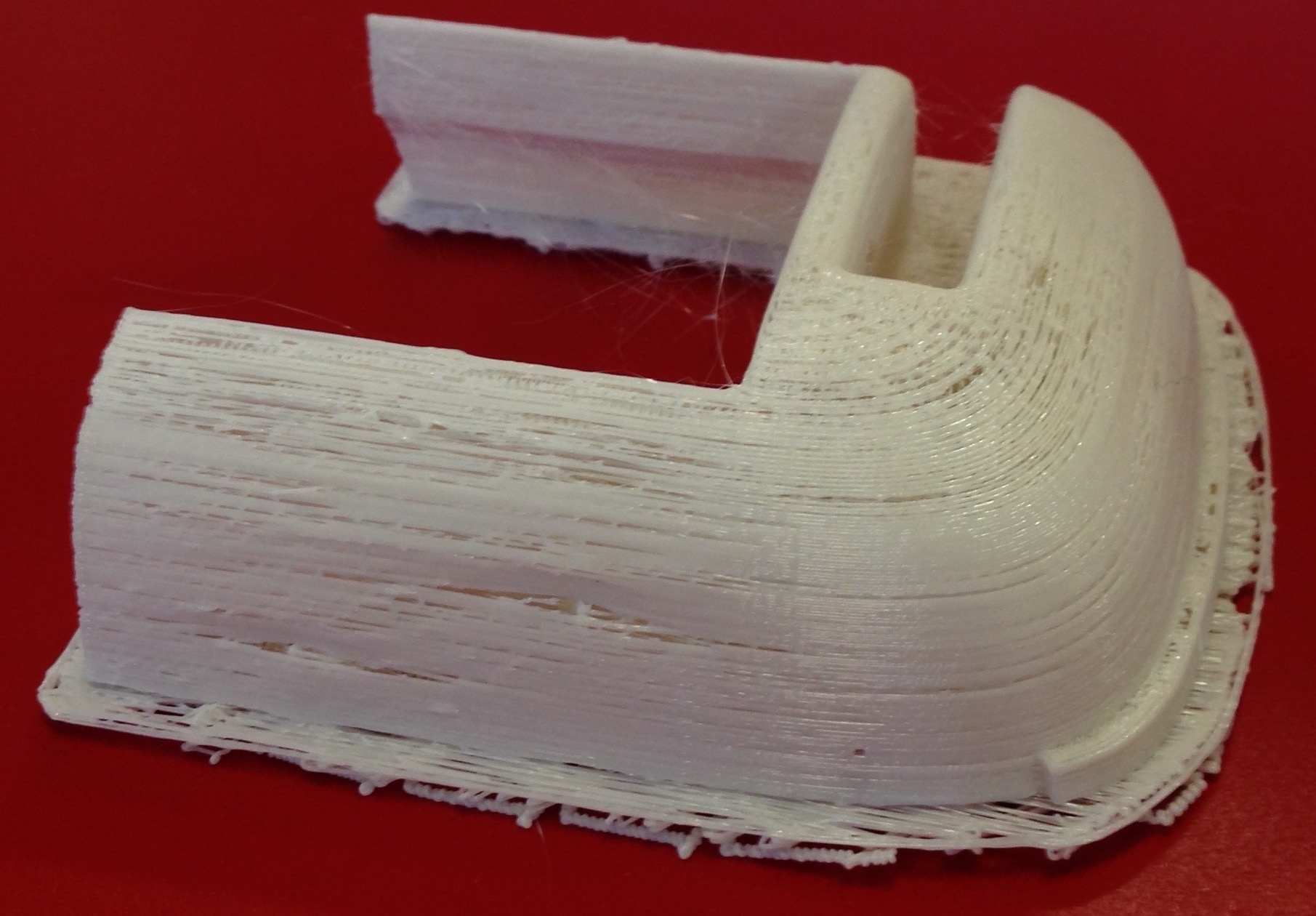
3D printing: support structure
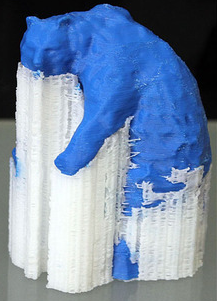
The defect on the overhanging feature is caused by insufficient support; support structure required.
SLA can print overhangs, but not local minima (e.g., bear hand).
3D printing: support structure removal
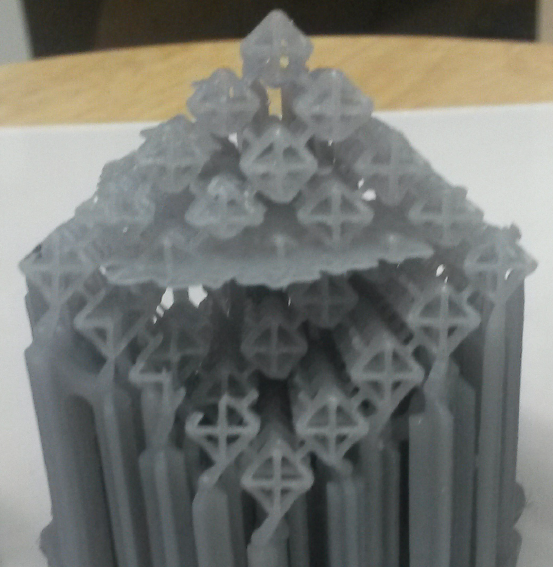
Removing support can be difficult or completely intractable.
3D printing: support structure for SLS
3D Hubs
SLS doesn’t need support structure!
3D printing: support structure for Multijet
3D Hubs
Multijet printers can print with dissolvable support!
3D printing: stringing and gaps (FDM)
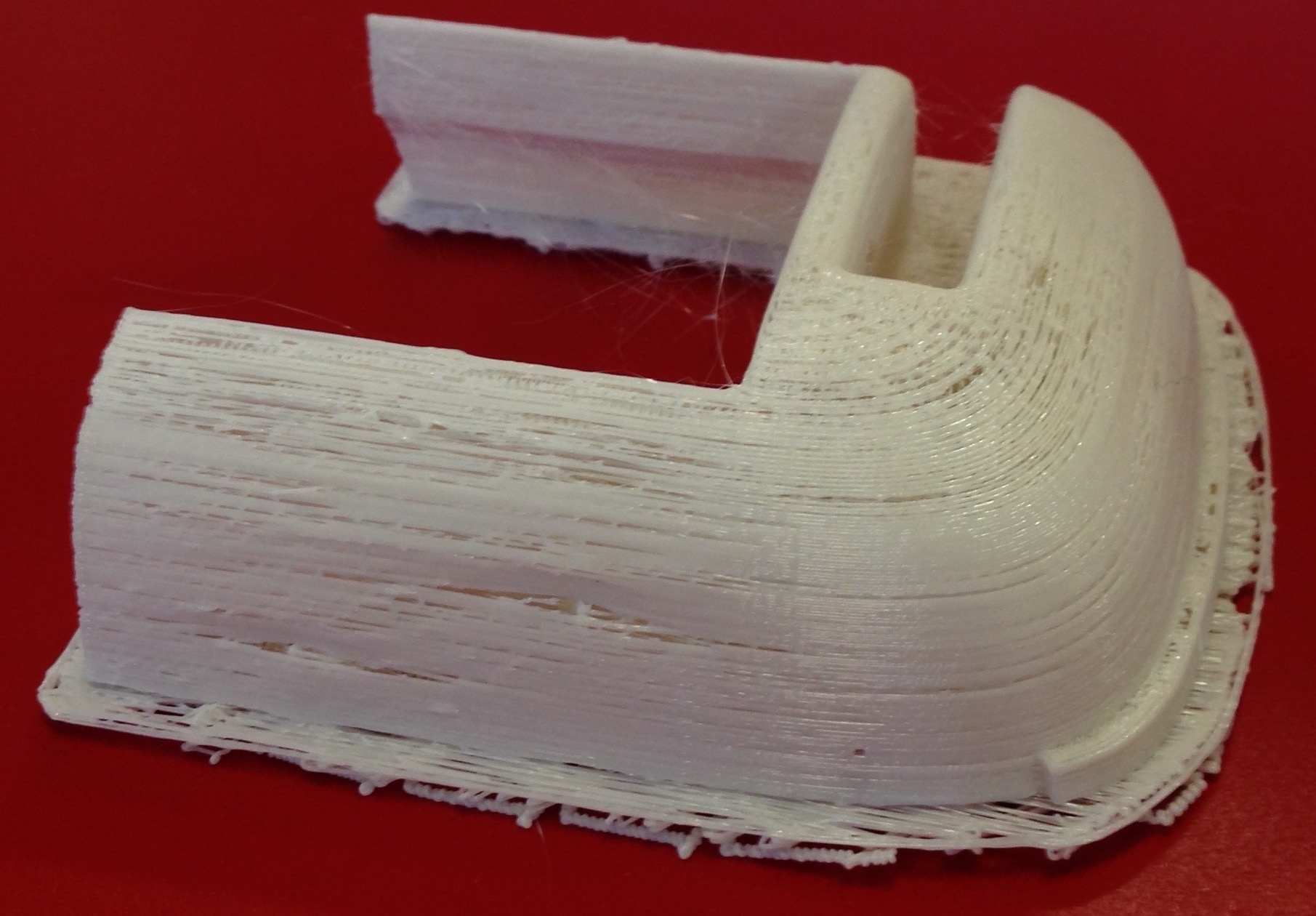
Stringing can be fixed by lowering temperature/speed or asking printer to retract filament.
Gaps can be fixed by increasing the extrusion rate.
3D printing: warping (FDM and SLA)

First few layers can warp/peel from build platform.
Consider printing on “raft.”
3D printing: design rules
- Minimum thickness constraints
3D printing: design rules
- Minimum thickness constraints
- Support requirements
3D printing: design rules
- Minimum thickness constraints
- Support requirements
- Clearance requirements
3D printing: design rules
- Minimum thickness constraints
- Support requirements
- Clearance requirements
- No enclosed voids (SLA/SLS)
Optimizing for 3D printing
What exactly can we optimize?
- Printing parameters
- Support structure
- The design itself
Optimizing printing parameters
- Adjust orientation/slicing to
- minimize print error
- keep prints fast: use adaptive slicing!
Optimizing support structure
Branching Support Structures for 3D Printing: Ryan Schmidt and Nobuyuki Umetani
These branching supports use 75% less material than the manufacture’s default support structure–reduce print time/cost.
(Note: part orientation matters here too!)
Minimize printing costs/maximize robustness
- Optimize printed design itself
- minimize printed volume without breaking
- maximize resilience for given print volume
- Cost-effective Printing of 3D Objects with Skin-Frame Structures
[Wang et al. 2013]
Fabrication services
Pushing 3D printing to the extremes
Large scale: concrete printers
Andrey Rudenko - Youtube
Pushing 3D printing to the extremes
Small scale: nanophotonics
Nanoscribe
Two photo lithography - nffa.eu
Microstructure with nanoscribe